Plasma cutting technology has been around for over half a century but has only recently gained widespread acceptance in the manufacturing industry. This is largely due to advances in technology which have drastically improved the quality and speed of the cutting process.
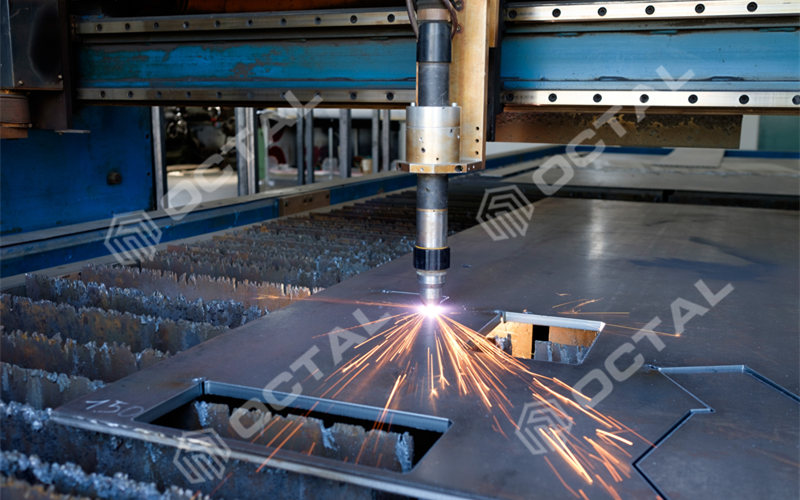
One company leading the way in this field is Penn Stainless Products. They provide powerful precision plasma cutting for up to 6.25-inch-thick stainless steel plate with a 10 feet wide x 65 feet long cutting envelope. This enables them to produce high-quality, intricate, and precise cuts in large volumes.
What is Plasma Cutting?
Plasma cutting is a process that uses a jet of ionized gas or plasma to cut through materials. The gas is heated to a very high temperature until it becomes ionized and can conduct electricity. This electricity forms an arc that melts and cuts through the metal.
The process is very precise, with plasma cutters capable of producing cuts as narrow as 0.1mm. This precision makes plasma cutting ideal for producing intricate designs and parts that require close tolerances.
What are the benefits of Plasma Cutting?
One of the main benefits of plasma cutting is its speed. Traditional cutting methods such as sawing or drilling can be slow and labor-intensive, especially when working with thicker materials. Plasma cutting can cut through thick metals quickly and accurately, reducing production time and costs.
Another advantage of plasma cutting is its versatility. It can cut through a wide range of materials, including stainless steel, aluminum, brass, and copper. This makes it a popular choice in the manufacturing industry, where materials can vary greatly depending on the product being produced.
Plasma cutting is also a relatively clean process, producing minimal waste and reducing the need for secondary clean-up operations. This makes it an environmentally friendly option in comparison to traditional cutting methods.
How is Plasma Cutting Revolutionizing the Manufacturing Industry?
Plasma cutting has revolutionized the manufacturing industry by making it possible to produce complex parts and designs quickly and accurately. This has opened up new possibilities for designers and engineers to create innovative products and structures that were previously impossible to produce.
One company taking full advantage of this is Hengli, a fully-integrated supplier of manufacturing and engineering services. They offer a range of services, including CNC plasma cutting, CNC flame cutting, laser cutting, bending, machining, and welding.
With over 160 employees, including Europe/US qualified certificate welders, and state-of-the-art 8 robot welding, Hengli is well-positioned to take advantage of the benefits of plasma cutting.
Enabling a high degree of accuracy and consistency in their manufacturing operations, they can produce high-quality parts and structures in large quantities. This has helped them to establish a competitive advantage in the marketplace, allowing them to offer their services at a lower cost than their competitors.
The Future of Plasma Cutting
As technology continues to advance, it is likely that plasma cutting will become even more common in the manufacturing industry. The ability to produce complex designs and parts quickly and accurately will continue to drive its adoption, making it an increasingly important part of the manufacturing process.
For companies such as Penn Stainless Products and Hengli, investing in plasma cutting technology has already paid dividends in terms of increased efficiency and cost savings. As more companies recognize its benefits, it is likely that plasma cutting will become a standard part of the manufacturing process.